The shape is not the only thing that differentiates prismatic and cylindrical cells. Other important differences include their size, the number of electrical connections, and their power output.
We’ll take a look at the core differences between cylindrical, prismatic, and pouch cells for batteries to understand how they interact with other tools and devices. Review a comparison of cylindrical cells with prismatic pouch cells. Look at the pros and cons of each type of battery packaging style, and learn some of the industrial uses that each kind of cell is best suited for.
Cylindrical vs. Prismatic vs. Pouch Cells – For anyone interested in the basic differences among cylindrical, prismatic, and pouch cells. Here’s a general breakdown of how and why these different battery packaging designs were created
Cylindrical Cells
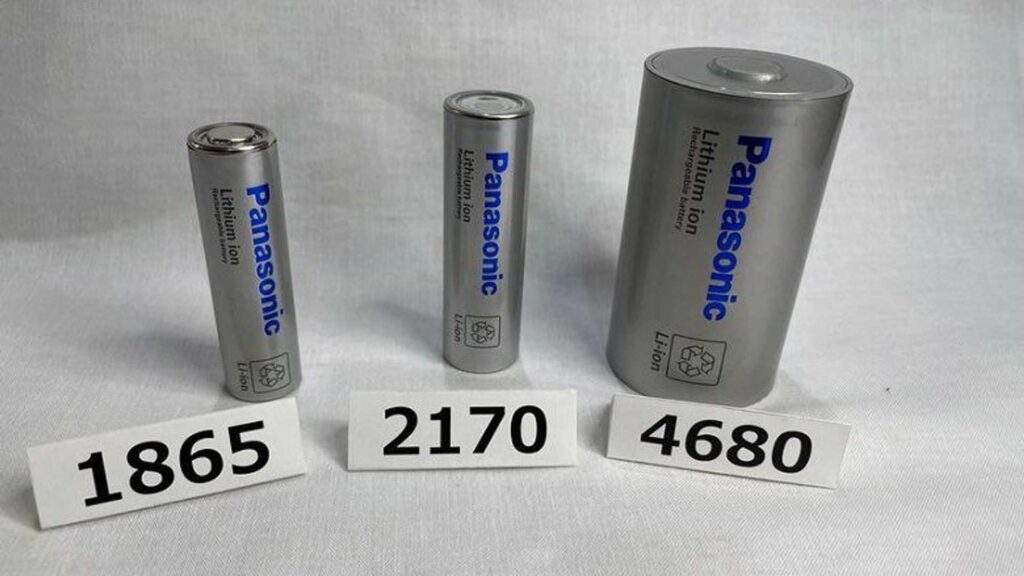
Tubular-shaped lithium-ion or nickel-based cylindrical cells number among the most popular batteries in use today. Their popularity stems from the fact that cylindrical cells are inexpensive to produce, widespread, stable, and safe to use. And can be applied uniformly across a variety of industries (i.e. they aren’t manufacturer-specific in shape and design).
Cylindrical lithium cells, which come with a very manageable watt-per-hour price, are a mainstay for portable gadgets and mobile tech. It’s probably a good idea to note that the electric car manufacturer Tesla has (literally) fueled the demand for cylindrical cells (18650 and the slightly larger 21700 cells). This demand is based on the company’s 2008 decision to use cylindrical cells. Instead of specially designed prismatic or pouch cells. That being said, Tesla isn’t 100% averse to using other types of batteries, as is the case for Tesla Model 3s made in China.
Prismatic Cells
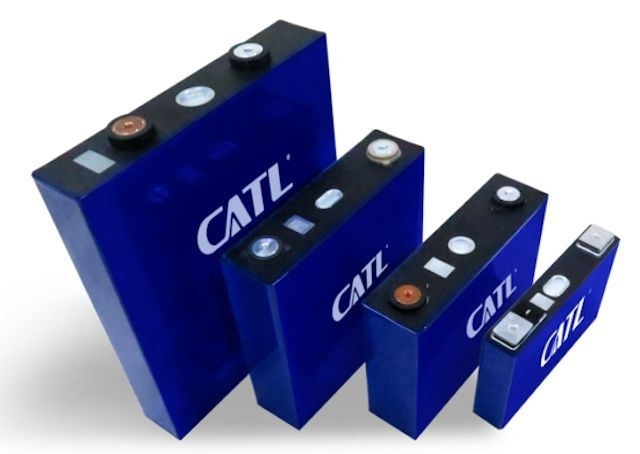
Lithium-ion (Li-ion) battery prismatic cells are thinner and lighter than cylindrical cells. These cells, coming in rectangular aluminum or steel casing (“cans” that increase stability), have fairly long lifespans.But aren’t as easy to keep cool compared to their cylindrical counterparts.
Prismatic cells, while thin and light, don’t come in a uniform, standard design. This fact means they can be quite costly to manufacture, coming with a higher watt-per-hour price point. Yet the prismatic cells’ variable shapes and sizes offer engineers more design flexibility, and the ability to layer them (thanks to their rectangular shape) They can limit the amount of valuable space they take up in products like mobile phones and tablets.
One disadvantage of prismatic cells is that if an issue arises with any one cell in a battery pack (likely due to thermal management difficulties), the entire pack will be in trouble.
However, the EV industry evolves quickly, and it’s uncertain whether prismatic cells or cylindrical cells will prevail. At the moment, cylindrical cells are more widespread in the EV industry. But there are reasons to think prismatic cells will gain popularity.
First, prismatic cells offer an opportunity to drive down costs by diminishing the number of manufacturing steps. Their format makes it possible to manufacture larger cells. Which reduces the number of electrical connections that need to be cleaned and welded.
Prismatic batteries are also the ideal format for the lithium-iron-phosphate (LFP) chemistry. A mix of materials that are cheaper and more accessible. Unlike other chemistries, LFP batteries use resources that are everywhere on the planet. They do not require rare and expensive materials like nickel and cobalt that drive the cost of other cell types upward.
There are strong signals that LFP prismatic cells are emerging. In Asia, EV manufacturers already use LiFePO4 batteries, a type of LFP battery in the prismatic format. Tesla also stated that it has begun using prismatic batteries manufactured in China for the standard range versions of its cars.
The LFP chemistry has important downsides, however. For one, it contains less energy than other chemistries currently in use and, as such, can’t be used for high-performance vehicles like Formula 1 electric cars. In addition, battery management systems (BMS) have a hard time predicting the battery’s charge level.
Pouch Cells
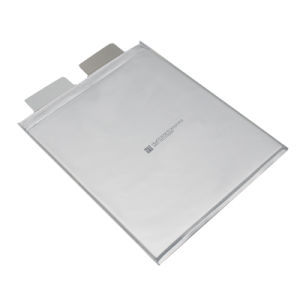
When comparing pouch cells with prismatic cells, one of the main differences to pay attention to is the lack of aluminum or steel casing. Instead, soft-pack pouch-cell lithium batteries are enclosed in a soft polymer aluminum plastic film or shell, which makes them very lightweight.
Lithium-polymer batteries (LiPo) make use of a polymer electrolyte rather than a liquid electrolyte. These batteries are increasingly popular with smartphone manufacturers. Their soft lightweight design also offers more safety measures than hard metal casings. When a critical issue with a pouch cell occurs – often due to internal pressure overheating or shortening the batteries – the pack will noticeably expand with gas. But the oversized pack won’t explode, which can happen with a hard aluminum or steel case.
High energy density pouch cells, due to their custom-built nature, light packaging, reliability, and small size are well-suited for automotive use, radio-controlled aircraft and cars, drones, and ultra-thin laptops.
Additionally, pouch cells are also used in technologies where weight and safety are an issue but a decent cycle life (how many times a battery or battery pack can be charged before it dies) and high energy density are also desired. Still, be aware that pouch cells cost more than lithium-ion batteries and often come with slightly less storage power, plus a shorter lifespan.
Comparing Cylindrical Cells with Prismatic Batteries and Pouch Cells
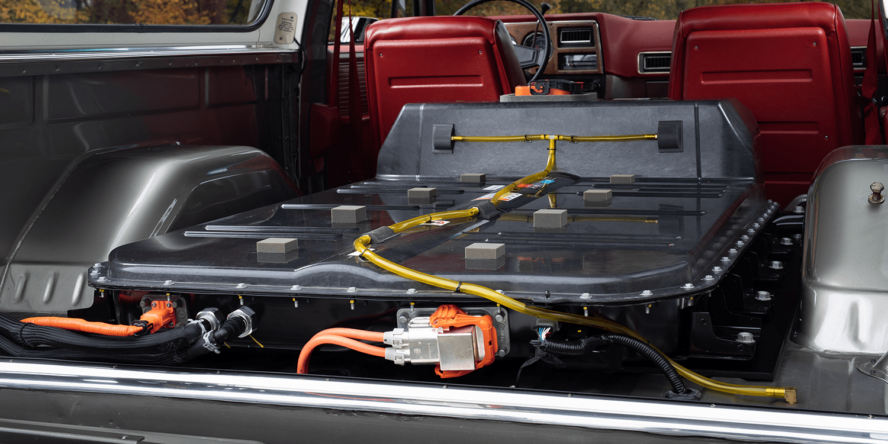
Now that you have some idea about the technology behind these different types of battery packaging. Let’s dive a little deeper into a comparison between cylindrical cells, prismatic batteries, and pouch cells.
Here are some of the main pros and cons you should look for when thinking about cylindrical vs. pouch cells. But of course, the type of cell you ultimately choose will depend on the type of application you need it for.
- Cylindrical cells, due to their widespread and standardized use. Offer a more robust automation process and better manufacturing techniques (providing a more consistent product) than pouch cells.
- Prismatic pouch cells are sensitive to deformation in high-pressure environments. Whereas cylindrical cells handle high internal pressures much better and without deforming.
- Cylindrical lithium battery electrodes are easier to weld when compared with lithium polymer pouch cells or prismatic cells.
- Pouch cells, while lightweight, are vulnerable to damage stemming from humidity and high temperatures. This can reduce their lifespans and increase their overall cost because they’ll need to be replaced more often.
- If a single cylindrical battery goes bad, the impact on the entire pack is relatively low. But with prismatic cells, if one battery goes bad, it can then compromise the entire pack.
- Cylindrical cells are stable, inexpensive, standardized across industries, and last a long time (thanks to better cycling). Prismatic cells and pouch cells are not standardized across industries, which makes them more expensive to produce. That said, their rectangular shapes utilize limited space better, and those with hard shells can be stacked. In most cases, softer pouch cells should not be stacked.
- Cylindrical batteries radiate heat and control temperature more effectively when compared to prismatic batteries. Prismatic batteries die faster due to less effective thermal management.
- The chemical activity at the edges and corners of prismatic batteries is rather poor. The less-than-optimal chemical activity of prismatic batteries means their performance decreases substantially after long-term use. Cylindrical batteries have a much longer lifespan compared to prismatic batteries.
Cylindrical cells, along with prismatic and pouch cells, all come with different advantages and disadvantages depending on their intended use. As battery packaging technologies change and continue to improve (e.g., removing rare and expensive cobalt from lithium-ion battery designs). These advantages and disadvantages will likely change as well.
The Main Differences Between Prismatic and Cylindrical Cells
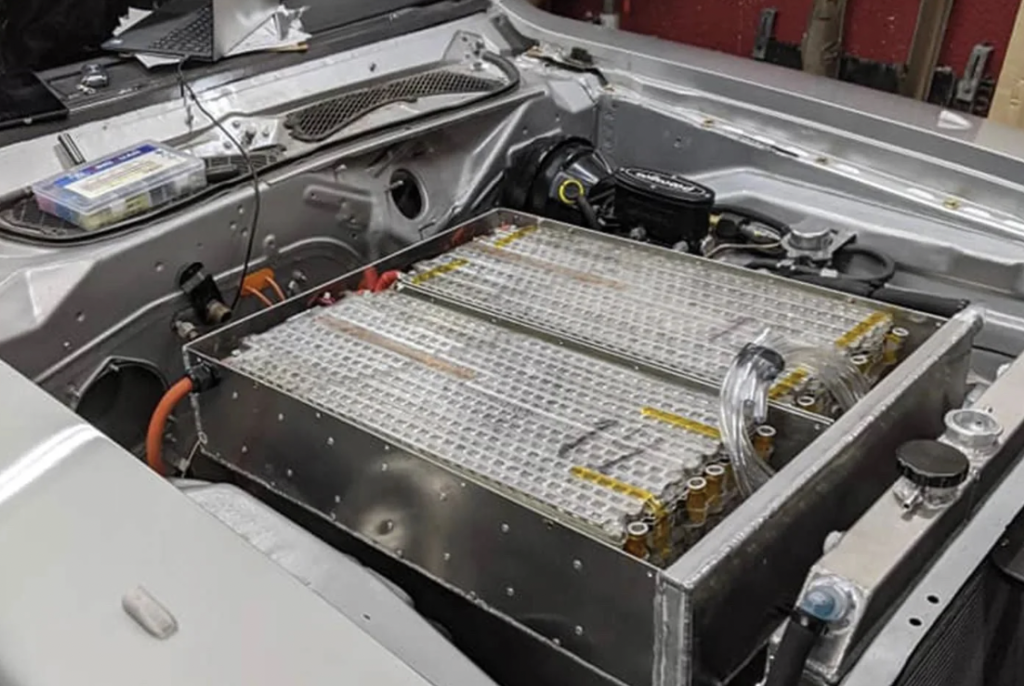
The shape is not the only thing that differentiates prismatic and cylindrical cells. Other important differences include their size, the number of electrical connections, and their power output.
Size
Prismatic cells are much larger than cylindrical cells and hence contain more energy per cell. To give a rough idea of the difference. A single prismatic cell can contain the same amount of energy as 20 to 100 cylindrical cells. The smaller size of cylindrical cells means they can be used for applications that require less power. As a result, they are used for a wider range of applications.
Connections
Because prismatic cells are larger than cylindrical cells, fewer cells are needed to achieve the same amount of energy. This means that for the same volume, batteries that use prismatic cells have fewer electrical connections that need to be welded. This is a major advantage for prismatic cells because there are fewer opportunities for manufacturing defects.
Power
Cylindrical cells may store less energy than prismatic cells, but they have more power. This means that cylindrical cells can discharge their energy faster than prismatic cells. The reason is that they have more connections per amp-hour (Ah). As a result, cylindrical cells are ideal for high-performance applications whereas prismatic cells are ideal to optimize energy efficiency.
Examples of high-performance battery applications include Formula E race cars and the Ingenuity helicopter on Mars. Both require extreme performances in extreme environments.
The best Lithium-ion cell type for your EV Swap depends on the specific application and usage requirements. Factors to consider include energy density, power density, cycle life, and cost. Some common types of Lithium-ion cells include Lithium Cobalt Oxide (LiCoO2), Lithium Manganese Oxide (LiMn2O4), Lithium Iron Phosphate (LiFePO4), and Lithium Nickel Manganese Cobalt Oxide (LiNiMnCoO2). Ultimately, the best type of Lithium-ion cell will depend on the intended use and the specific requirements of the application.